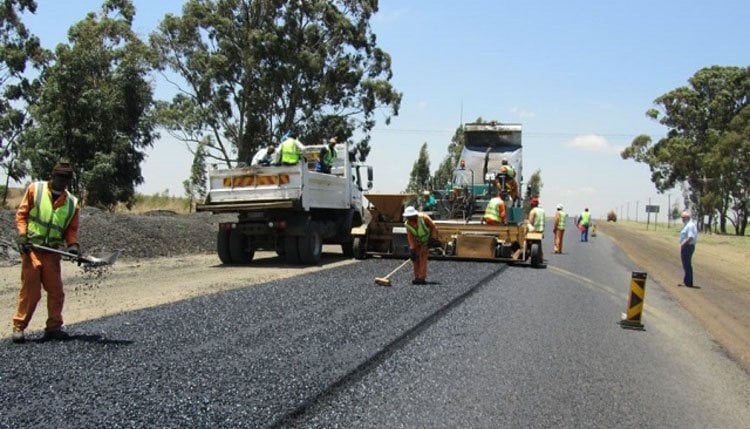
Roads maintenance, repair and rehabilitation
27 March 2019Table of Contents
Roads maintenance, repair and rehabilitation
Roads are exposed to tremendous loads that will sooner or later leave their marks on them. A time will come when every road will be in need of a general overhaul. But no two damage patterns are alike.
Which rehabilitation methods offer a cure for distressed roads? What are the differences between them? Which are suitable to be carried out as mobile roadworks?
Replacing the pavement
Replacing the pavement is a standard procedure when repairing roads. The challenge is to ensure that only the damaged layers of the road structure are removed – and to avoid disruptions to traffic at the same time. Under these conditions, cold milling is the only viable option for many construction projects
The tools that cold milling machines use for removing road layers were originally developed for the mining industry. So-called point-attack cutting tools, fitted to a rotating milling drum on the underside of the machine, bite into the road at precisely the specified depth.
Fine milling
Fine milling is an alternative to time-consuming and expensive complete rehabilitation. This method is used above all when traffic safety is severely compromized by undulations, ruts or a slippery surface.
Many countries are investing less money in maintaining their road network despite increasing traffic loads. The result is a growing demand for fast and economically efficient solutions that are capable of taking the edge off hazardous stretches of road.
Fine milling is such a method, and is predominantly used where bumps and wheel ruts, or slippery surfaces pose an acute danger to traffic safety.
Paving thin layers hot
It is not necessary to replace the entire pavement if only the surface of the roadway shows signs of damage. The method known as “paving thin overlay hot on hot” is a particularly economical and eco-friendly alternative.
Rehabilitation methods that can be carried out both quickly and with economic efficiency are becoming increasingly important worldwide. Paving thin layers in hot application is such a method, offering an exceptionally economical alternative to full pavement rehabilitation.
Paving thin layers in hot application is eminently suitable for roads in need of rehabilitation but with damages limited to the surface, or poor grip, or pronounced surface irregularities. The surface properties of worn-out roads, such as grip, evenness and noise reduction, can be improved significantly for extended periods of time.
Paving thin layers cold
“Thin overlays paved cold on cold” – better known abroad as “micro-surfacing” – are another quick and cost-effective alternative to replacement of the complete pavement.
Mixing and laying machines spread the mixture for the thin cold layer over the fine-milled surface with Vario screeds.
Traffic safety is jeopardized when the road surface gets slippery, when wheel ruts have dug into the pavement, or when the road is covered with bumps and deformations. Paving thin layers in cold application is a method that is increasingly used for restoring road surfaces to good evenness and skid resistance. Known as “microsurfacing” in many countries around the globe, paving thin layers in cold application prolongs the service life of damaged asphalt roads without the need for replacing the entire road pavement.
InLine Pave
InLine Pave has become established as an official construction method according to German regulatory frameworks. The binder and surface courses are paved “in line”, i.e. one after another “hot on hot” in a single pass. Since the machines are just 3 m wide, traffic can continue to flow without obstruction on the remaining lanes.
Hot recycling
Porous and deformed surface courses can be rehabilitated by hot recycling, a process which is exclusively applied in the form of a mobile construction site. An intact layer structure is essential here. Hot recycling improves all relevant properties of the surface and roadway profile, as well as the composition of aggregate fractions in the surface course.
The surface course is heated up to 150 °C by a panel heating machine with gas-fired infrared heating panels so that the hot recycler can then scarify, remove, process and repave the softened asphalt. In this way, the road’s non-skid properties can be restored, water can run off again and ruts are eliminated. The potential savings are enormous.
Cold recycling in-situ
Cold recycling in-situ is just the right technology when it comes to building a new road from old. It is mostly carried out as mobile roadworks. What are the advantages of “in-situ” cold recycling? How does the method work?
The cold recyclers stand out thanks to their ease of operation with new automatic functions, main control panels that can be positioned as required, and an on-board diagnostic system.
The sub-base of roads exposed to major stresses due to heavy goods traffic is often damaged. To remedy this damage, the complete road structure must be repaired. Cold recycling restores the roads’ stability.
The difference between “in plant” and “in situ” cold recycling is that, in the latter case, the entire process takes place in a single operation.
This is what happens: special cold recyclers granulate the defective layers – usually the surface and binder course, as well as part of the base course – mix the reclaimed asphalt pavement with fresh binder and replace it immediately. The advantages of this method are short construction times and high cost efficiency.
Cold recycling in-plant
When cold recycling road pavements, contractors can choose between processing the milled material “in-situ”, meaning on the job site, or “in-plant”, meaning in a cold mixing plant. Their decision is influenced, however, not only by the damage patterns of the road to be repaired. What are the advantages offered by “in-plant” cold recycling? How does it work? What kinds of damage patterns can cold recycling “in-plant” be used for?
A typical application: the KMA 220 is positioned in the direct vicinity of the material storage area.
One speaks of cold recycling “in-plant” when the reclaimed asphalt material of roads in need of rehabilitation is recycled in a nearby mixing plant, transported back to the job site, and then placed again by road pavers. The method is often used with roads that are exposed to high loads by heavy traffic, and with damages extending all the way into the pavement subgrade, but where site conditions do not allow the operation of an “in-situ” cold recycling train.
Source : www.wirtgen-group.com