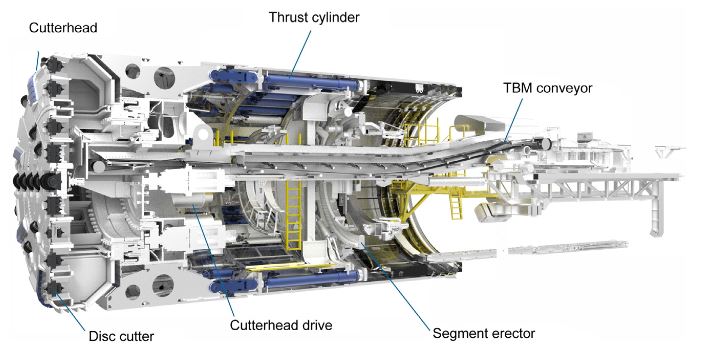
Tunnel Boring Machine Types
11 May 2021Table of Contents
Tunnel Boring Machine Types
There are several types of TBMs. The best TBM for a project is based on the geological conditions of the site and the project’s features.The general classification of the different types of TBMs for both hardrock and soft ground are presented here.
Fig 1. TBM’s Classification
1. Gripper Tunnel Boring Machine
A gripper TBM is a rock tunnel boring machine which generally utilizes roller disc cutters as excavation tools and which moves forward by reacting (i.e., exerting shove forces) against the tunnel walls through a hydraulic gripper reaction system.
It is is suitable for driving in hard rock conditionswhen there is no need for a final lining. The rock supports (rock anchors, wire-mesh, shotcrete, and/or steel arches) can be installed directly behindthe cutter head shield and enable controlled relief of stress and deformations.
The existence of mobile partial shields enables gripper TBMs to be flexible even in high-pressure rock. This is useful when excavating in expanding rock to prevent the machine from jamming.
Fig 2. Typical diagram of an open gripper main beam TBM.Courtesy of TheRobbins Company
2. Double-Shield Tunnel Boring Machine
A double-shield TBM is generally considered to be the fastest machine for hard rock tunnels under favorable geological conditions with installation of the segment lining. It is possible to drive 100 m in 1 day. This type of TBM consists of a rotating cutter head and double shields (Fig. 3), a telescopic shield (an inner shield that slides within the large router shield), and a gripper shield together with a shield tail.
While boring, gripper shoes radially press against the surrounding rock to hold the machine in place and take some of the load from the thrust cylinders. For the motion of the front shield the gripper shoes are loosened, before the front shield is pushed forward by thrust cylinders protected by the extension of the telescopic shield.
Because regripping is a fast process, double-shield TBMs can almost continuously drill. As for the shield tail, it is used to provide protection for workers while erecting,installing the segment lining, and pea grouting.
Fig 3. Typical diagram of a double-shield TBM.Courtesy of The Robbins Company
3. Single-Shield Tunnel Boring Machine
Single-shield TBMs (Fig. 4) are used in soils that do not bear ground-water and where rock conditions are less favorable than for double shields, such as in weak fault zones. The shield is usually short so that a small radius of curvature can be achieved.
Fig 4. Typical diagram of single-shield TBM.Courtesy of The Robbins Company
4. Earth Pressure Balance Machines
Earth pressure balance (EPB) technology (Fig. 5) is suitable for digging tunnels in unstable ground such as clay, silt, sand, or gravel. An earth paste face formed by the excavated soil and other additives supports the tunnel face. Injections containing additives improve the soil consistency, reduce soil stick, and thus its workability.To ensure support pressure transmission to the soil, the earth paste is pressurized through the thrust force transfer into the bulkhead.
The TBM advance rate (in flow of excavated soil) and the soil outflow from the screw conveyor regulate the support pressure at the tunnel face. This is monitored at the bulkhead by the readings of pressure sensors.
Fig 5. Scheme of an EPB machine
5. Slurry Tunnel Boring Machine
Slurry TBMs are used for highly unstable and sandy soil and when the tunnel passes beneath structures that are sensitive to ground disturbances. Pressurized slurry (mostly bentonite) supports the tunnel face. The support pressure is regulated by the suspension inflow and outflow. The slurry’s rheology must be chosen in accordance with the soil parameters and should be carefully and regu-larly monitored.
6. Mixshield Technology
Mixshield technology (Fig. 6) is a variant of conventional slurry technology for heterogeneous geologies and high water pressure. In mixshield technology an automatically controlled air cushion controls the support pressure, with a submerged wall that divides the excavation chamber.This wall seals off the machine against the excess pressure from the tunnel’s face. As air is compressible in nature, the mixshield is more sensitive in pressure control and thus will provide more accurate control of ground settlement.
Fig 6. Overview of a mixshield TBM.Courtesy of Herrenknecht AG
7. Pipe Jacking
Pipe jacking (also called microtunneling) is a micro- to small-scale tunneling method for installing underground pipelines with minimum surface disruption. It is used for sewage and drainage construction, sewer replace-ment and lining, gas and water mains, oil pipelines, electricity and telecommunications cables, and culverts .
A fully automated mechanized tunneling shield is usually jacked forward from a launch shaft toward a reception shaft. Jacking pipes are then progressively inserted into the working shaft. Another significant difference between the pipe jacking method and shield method is that the lining of the pipe jacking is made of tubes and the lining of the shield method is made up of segments. In order to significantly reduce the resistance of the pipes, a thixotro-pic slurry is injected into the outside perimeter of the pipes. The thixo-tropic slurries can also reduce disturbance to the ground while pipe jacking slurry thickness. The thickness should be six to seven times thevoid between the machine and pipes.
Fig 7. Typical Components of a Pipe Jacking Operation
8. Partial-Face Excavation Machine
Partial-face excavation machines (Fig. 8) have an open-face shield andcan sometimes be more economical in homogeneous and semistable ground with little or no groundwater. In boulders layer, the open-face can deal with boulders much easier than closed shield machines. In cavity ground, the open-face can avoid the risk of falling down into the bottom of the cavity. Thanks to their simple design and that the operator workplace is close to the open tunnel face, these machines can easily be adapted to changing geological conditions. Good excavation monitoring can also be carried out.
Fig 8. Two kinds of partial-face excavation machines.Courtesy ofHerrenknecht AG